Summary
- The Airbus A350 was a response to Boeing’s fuel-efficient 787 Dreamliner.
- Qatar Airways placed a significant order for the Airbus A350, prompting a major design change.
- Components for the A350 are manufactured in various locations worldwide and then assembled in Toulouse.
To understand where all the parts that go into building the Airbus A350 are made, you must first grasp the company’s vision and learn how it came to be. In the 1960s, European planemakers needed help competing with American giants like Boeing, Lockheed, and McDonnell Douglas. To counter the American giants, Aerospatiale-Matra of France, DASA from Germany, and later British Aerospace joined forces to create what is now a European multinational aerospace corporation with factories in many countries.
The name “Airbus” was chosen from a non-proprietary term used by the airline industry in the 1960s to refer to commercial aircraft of a specific size and range, and was also linguistically acceptable to the French. Noticing a niche for a short-to-medium-range, high-capacity airliner, the result would be the Airbus A300, the world’s first twin-engine, double-aisle widebody airliner. Airbus designates its aircraft with the letter A and then a number beginning with 3 because the A300 was initially designed to seat 300 passengers. To help strengthen the brand, every aircraft after the A300 has also used the A3XX format.
The Airbus A350
Following the September 11, 2001, terrorist attacks and increased fuel costs, airlines prioritized fuel efficiency over speed. Before 9/11, Boeing was working on the “Sonic Cruiser” aircraft that could fly at Mach 0.98 with the same fuel burn as a Boeing 767. After officially canceling the Sonic Cruiser on December 20, 2002, Boeing began working on a small, midsize, wide twin-engine aircraft ideal for point-to-point flights. Using technology from the Sonic Cruiser, the new Boeing 787 Dreamliner offers airlines an alternative to hub-and-spoke operations.
Photo: Boeing
Airbus, meanwhile, was not worried and did not see Boeing’s new widebody twinjet as a threat to its Airbus A330. However, airlines liked the efficiency of the Boeing 787 Dreamliner, forcing Airbus to develop a plane that could compete. Using a mostly carbon fiber-reinforced polymer wing and new engines, engineers at Airbus calculated that the A350 would be 10% more efficient than the A330.
Qatar Airways orders 60 Airbus A350s
On June 13, 2005, while visiting the Paris Air Show, Gulf State carrier Qatar Airways placed an order with Airbus for 60 A350s. Initially, Airbus planned to make what would essentially be an A330 with composite wings and new engines. The planemakers’ two largest customers, the International Lease Finance Corporation (ILFC) and GE Capital Aviation Services (GECAS) called the move “a Band-aid reaction to the 787”, forcing Airbus to come up with a clean sheet design. At the Farnborough International Airshow the following summer, Airbus revealed the new aircraft called the “A350 XWB” (Xtra-Wide-Body). Singapore Airlines liked the latest design and placed an order for 20 aircraft.
The Airbus A350 made its maiden flight from Toulouse–Blagnac Airport (TLS) on June 14, 2013, and then entered service with launch customer Qatar Airways on January 15, 2015.
Airbus has factories worldwide
Image: Cathay Pacific
While most people think of Airbus as a French company because all of its widebody aircraft are assembled in Toulouse, the truth is that the components that make up the Airbus A350 come from around the world.
Airbus Broughton, United Kingdom
Occupying a 700-acre site in northwest England, the Airbus factory in Broughton builds wings for the Airbus A350 in four separate buildings. The site Airbus chose to build the factory on has its own airport and an aviation pedigree dating back to when it was used to build the WWII Avro Lancaster heavy bomber.
Photo: Cathay Pacific
Once the wings are built, they are loaded aboard a large specially designed cargo variant of the Airbus A330 called the Beluga XL and then flown to Breman, Germany.
Airbus Bremen, Germany
What was once the Focke-Wulf-Flugzeugbau AG engineering works covers the size of 64 football fields and is now responsible for fitting the wings’ hydraulic lines and electrical cables. Eight days after arriving in Bremen, the wings are put aboard a Beluga XL and flown to Toulouse, France, for final assembly.
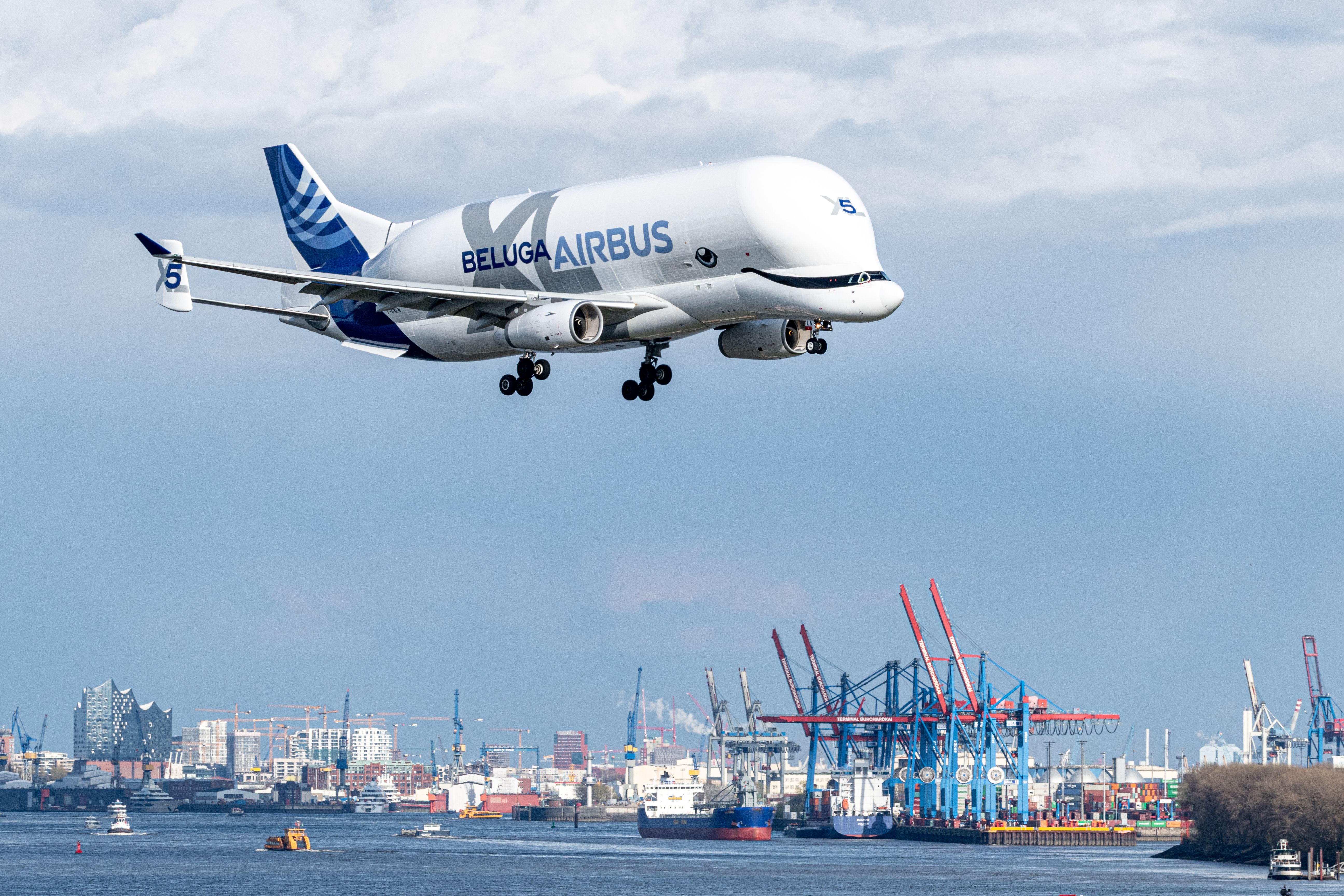
Related
Tracking Airbus’ Beluga XL Fleet: How To See Where They Fly
Social media channels also track aircraft like Airbus BelugaXL.
Airbus Hamburg, Germany
Located at Hamburg Finkenwerder Airport (XFW), Airbus Hamburg is the final assembly line for all Airbus A320 family aircraft. In addition to the A320, Hamburg builds the rear fuselage and vertical tail plane for the Airbus A350 and A330. Once finished, a Beluga XL flies the parts to Toulouse.
Airbus Gloucester, United Kingdom
At its plant in its Gloucester facility near the Cotswolds, Safran Landing Systems builds the main landing gear and brakes for the Airbus A350-900. The facility typically produces eight monthly systems on the A350-900, but it can sometimes be as many as ten. Once ready, the landing gear is loaded aboard a Beluga XL and flown to Toulouse.
Airbus Atlantic Saint-Nazaire, France
Airbus builds the forward and center fuselages for the Airbus A350 at its Saint-Nazaire plant. Once built, they are sent to Toulouse for final assembly.
Airbus Getafe, Spain
At its plant in the Getafe suburb of Madrid, Airbus manufactures the horizontal tail planes used on all Airbus aircraft, including the 204.5-foot-wide tail plane used on the A350-900 and A350-1000. Once built, they are sent to Toulouse for final assembly.
Rolls-Royce, Derby, England
Rolls-Royce supplies Airbus with its Trent XWB high-bypass turbofan engine, which is specially designed, engineered, and optimized to power the Airbus A350.
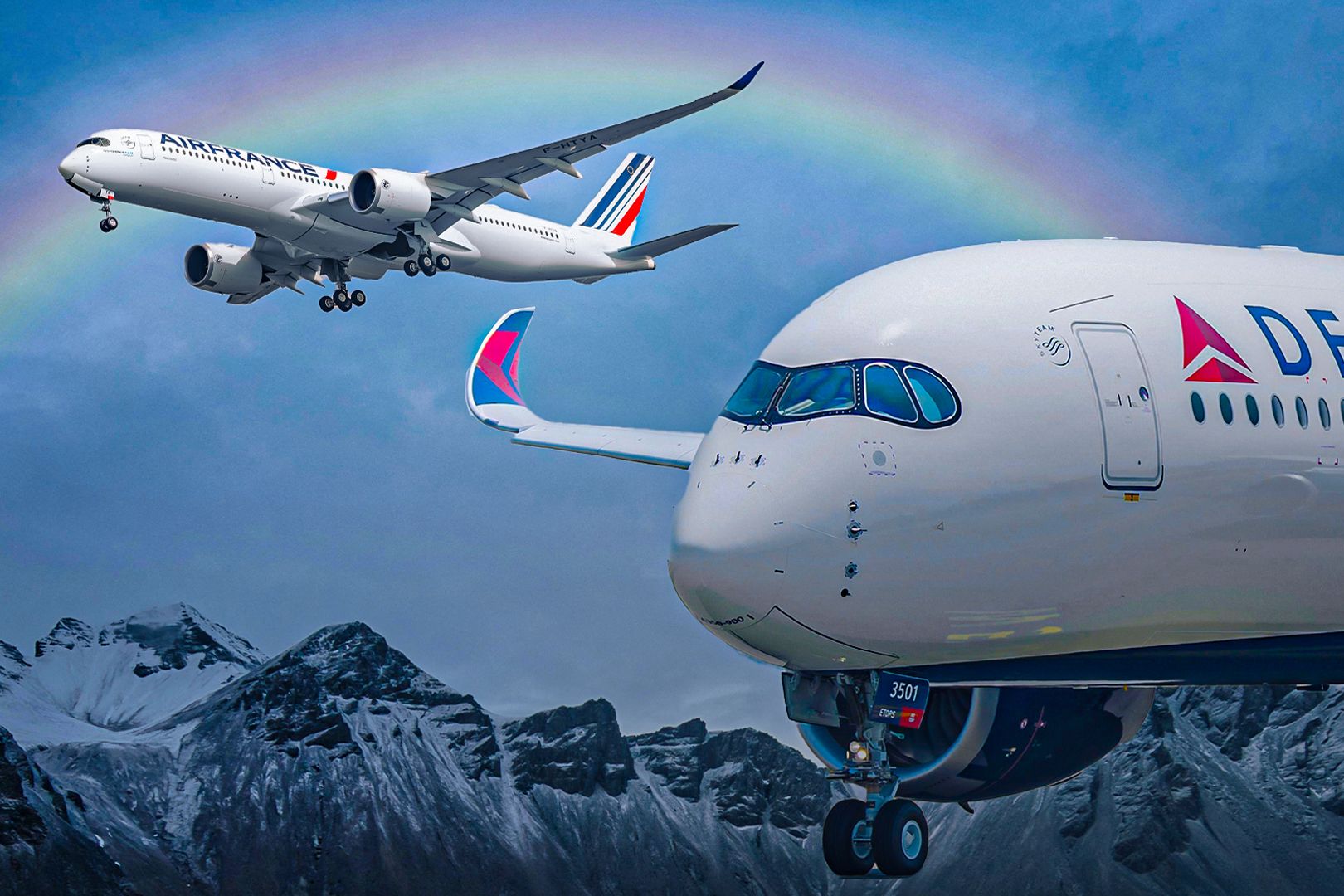
Related
Analysis: Which Carriers Operate The Most Airbus A350 Flights To, From & Within The US?
Delta, Iberia, and Turkish are some of the most popular names in this list.