Photo: Boeing
Summary
- Solved battery issues after fires in 2013, with changes to safety and approval processes.
- Rolls-Royce fixed the blades of the Trent 1000 engines, eradicating cracking and corrosion.
- Boeing tackled manufacturing issues with hairline wing cracks, ensuring no impact on delivery.
First introduced in late October 2011 with Japanese carrier ANA, Boeing’s 787 Dreamliner is famous for many of its initial technologies. Extensively using composite materials, packing various fuel-saving features such as hybrid laminar flow control, and utilizing several advanced electronic controls, the widebody jet is an incredible piece of engineering.
Yet, it’s not without its set of issues. In some ways, the Boeing 787 is infamous for multiple series of incidents, failures, and, most recently, quality control issues. Given the Everett-based manufacturer’s long history in the business, it’s not surprising that, in due time, these things get worked out, and airlines have been taking deliveries of 787 family airliners for much of the year. Let’s take a look at a few things that have changed over the last 13 years regarding the widebody jet’s production and development.
1
A redesigned battery
Several battery-related fires early in the program led to jet grounding
Date |
2013 |
---|---|
Area of concern: |
Cell 5 or Cell 6 of the APU Battery |
Issue: |
Recurrent fires starting from onboard Lithium-ion batteries |
Fix: |
Adjustments to better contain battery system fires |
Many people familiar with the situation will know that within a couple of years of the Boeing 787’s introduction, multiple onboard fires were caused by an issue with the aircraft battery. After three incidents, the last one involving an emergency landing leading to multiple sustained injuries, the type was grounded until the manufacturer could devise a solution. Japanese flag carrier ANA reported losing $1.1 million per day while the jet was grounded, according to reporting from Reuters.
Photo: Boeing
Boeing was able to provide a solution in just a few weeks that would eventually appease the FAA and un-ground the airliners. According to a statement from the time, production and testing procedures would incorporate more strict screening of the battery cells before assembly. For thermal and electrical adjustments, the system’s voltage range would be enhanced, and a specialized enclosure would prevent fires from ever even starting.
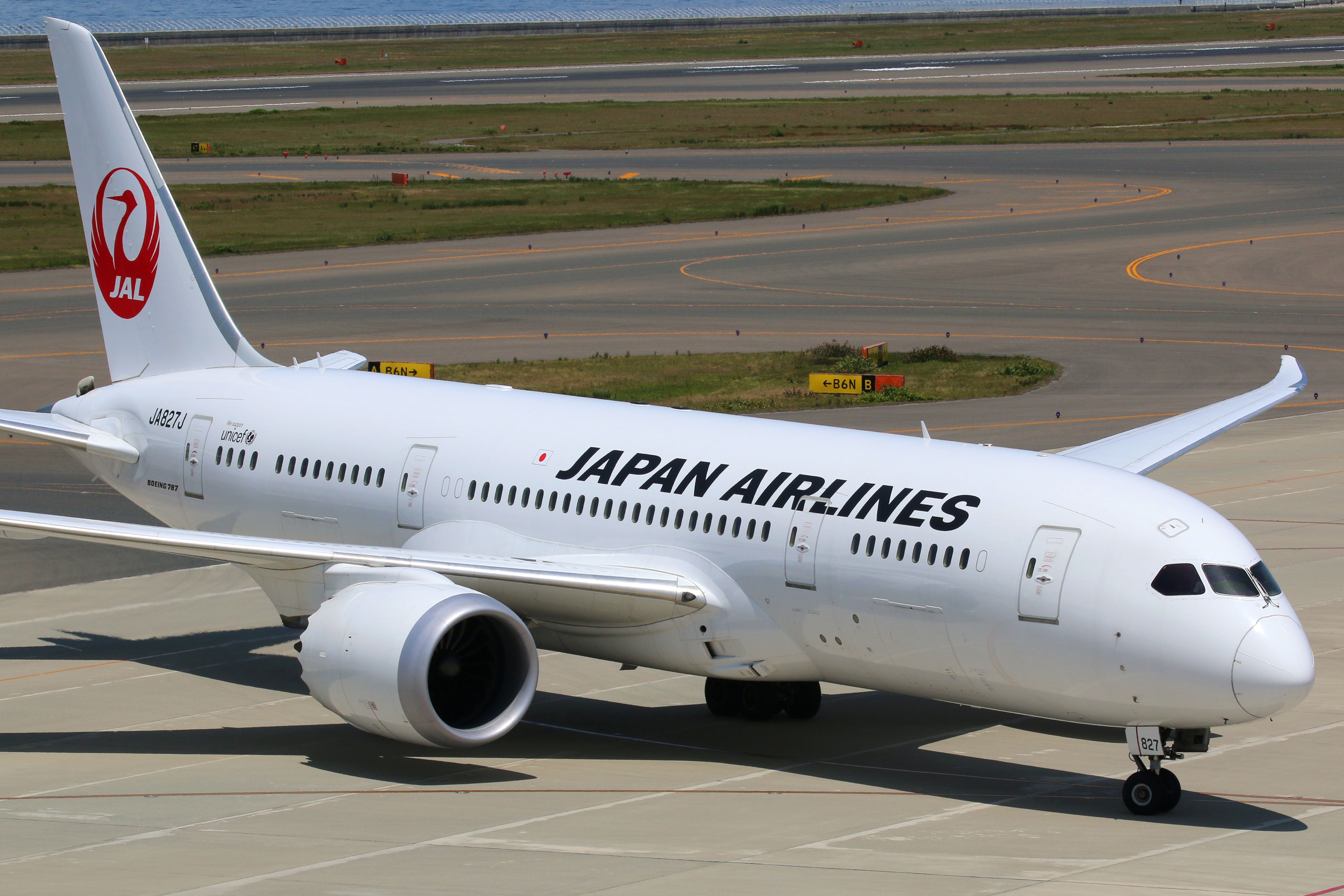
Related
What Caused The Battery Fires That Grounded the Boeing 787 10 Years Ago?
A combination of design issues, wrong assumptions, and inadequate testing procedures contributed to the fleet’s grounding.
2
Changes to Rolls-Royce’s Trent 1000 engines
Early corrosion was quickly fixed by Boeing
Date |
2019 |
---|---|
Area of concern: |
Rolls-Royce Trent 1000 engines |
Issue: |
Premature corrosion of engine fan blades |
Fix: |
Adjustments to blades to prevent cracking and corrosion |
In 2019, several Boeing 787s had to be grounded because of an engine issue. Rolls-Royce provides its Trent 1000 model to power the widebody airliner. It had even been enhanced over the years, with the British engine manufacturer producing the “Trent 1000 TEN” with better fuel burn than the Package C and was a highly competitive option against GE’s popular GEnx engine.
Photo: Maxene Huiyu | Shutterstock
Unfortunately, much farther ahead of expectations, customers noticed corroding and cracking engine blades on their Trent 1000-equipped Dreamliners. However, Rolls-Royce was able to fix its issues by solving the sulfidation issue of the intermediate-pressure turbine blades and redesigning the High-Pressure turbine blades. Notably, Rolls-Royce was able to get through the entire backlog of grounded 787s within a year.
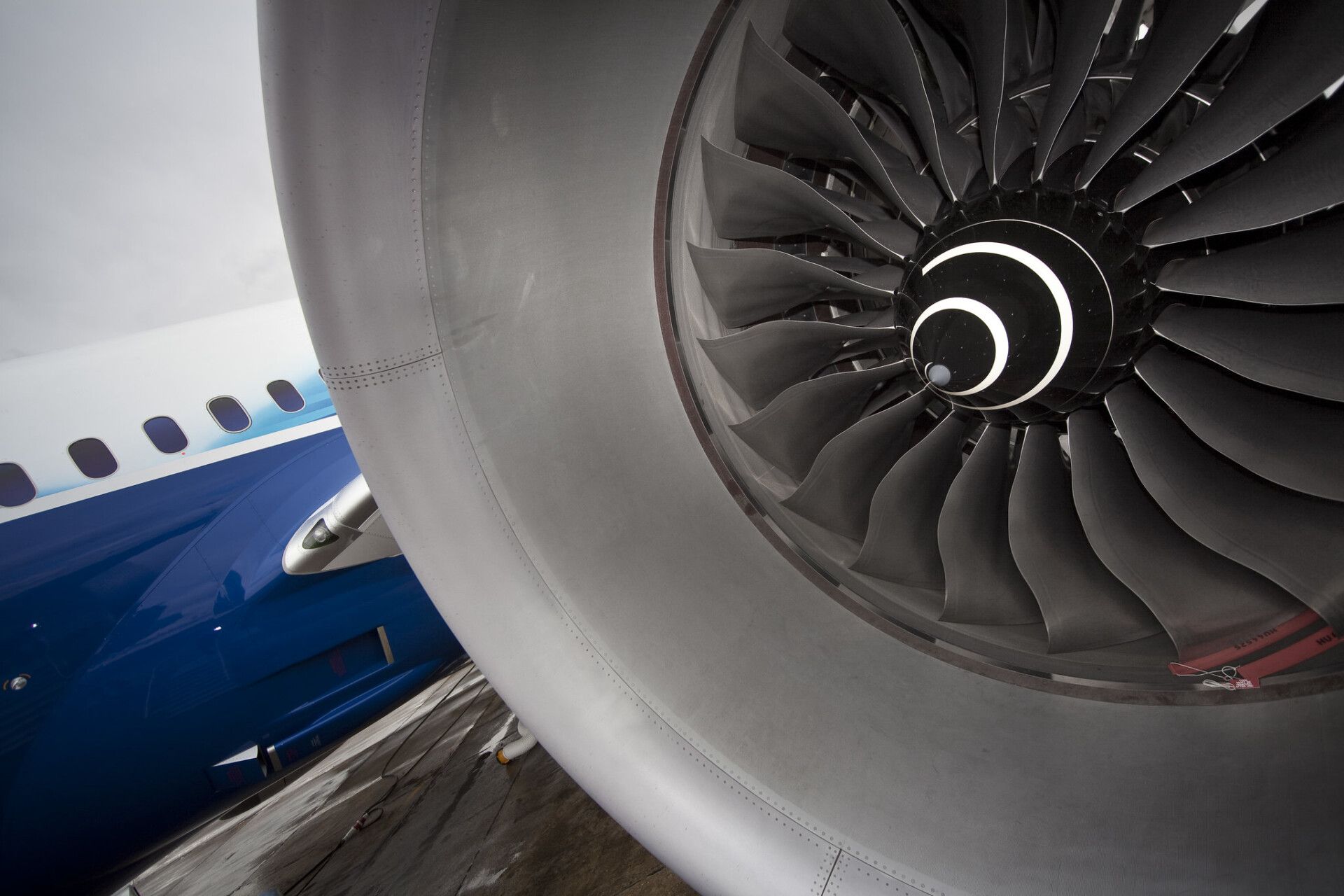
Related
How Rolls-Royce Solved Its Trent 1000 Issues
3
Wing manufacturing adjustment
Hairline cracks were found in 2014 after Mitsubishi manufacturing changes, but only affecting aircraft in production
Date |
2014 |
---|---|
Area of concern: |
Wings |
Issue: |
Hairline cracks found in wing ribs |
Fix: |
Changes to the manufacturing process – issue only affected aircraft in production |
In March 2014, Boeing reported that hairline cracks were found in current-production examples of the widebody aircraft. The concern here was that these would enlarge over time and cause further issues. Confident the production issue did not affect any Dreamliners operating at the time, something had to be done about the dozens of models that were not quite at the end of their manufacturing process.
Photo: Dewa Ketut Partana/Shutterstock
Mitsubishi Heavy Industries, in charge of making the carbon composite wings in Japan, was the company that tipped off the Washington-based planemaker. It was realized that something about its manufacturing process was the root cause of the cracks found in a number of shear ties on 787 wing ribs. A couple of weeks of work were spent inspecting the suspected damaged wings while the Japanese manufacturing process could be altered. Boeing said in a statement at the time:
“The affected areas are very small and the time required to address the issue will vary between one and two weeks. There may be some delays in deliveries, but we expect no impact to 2014 delivery guidance.”
4
All-new titanium parts
Working with Norsk Titanium on new 3D-printed parts fixed quality issues and saved money on construction
Date |
2017 |
---|---|
Area of concern: |
Fuselage plates |
Issue: |
Improperly manufactured titanium parts |
Fix: |
Partnership with new supplier |
Although the 787 is made up of 80% composites by volume, this is only about 50% by weight. Another 15% of the weight comes in the form of titanium, an incredible yet extortionate metal. To save a significant amount of money, in 2017, Boeing partnered up with the Norwegian-based Norsk Titanium to come up with a solution to its titanium needs.
Photo: Thiago B Trevisan | Shutterstock
By utilizing 3D-printed metal parts, Boeing estimated a cost saving of up to $3 million USD per Dreamliner. 3D printing is not a novel industry solution, with companies such as GE utilizing this manufacturing process to reduce 300 engine parts to just seven.
Interestingly, though somewhat unrelated, Boeing had an issue with other titanium parts found in one of the 787’s fuselage sections. These components were provided by a different 3rd party supplier, who confirmed the problem upon an audit carried out by the US-based aircraft manufacturer.
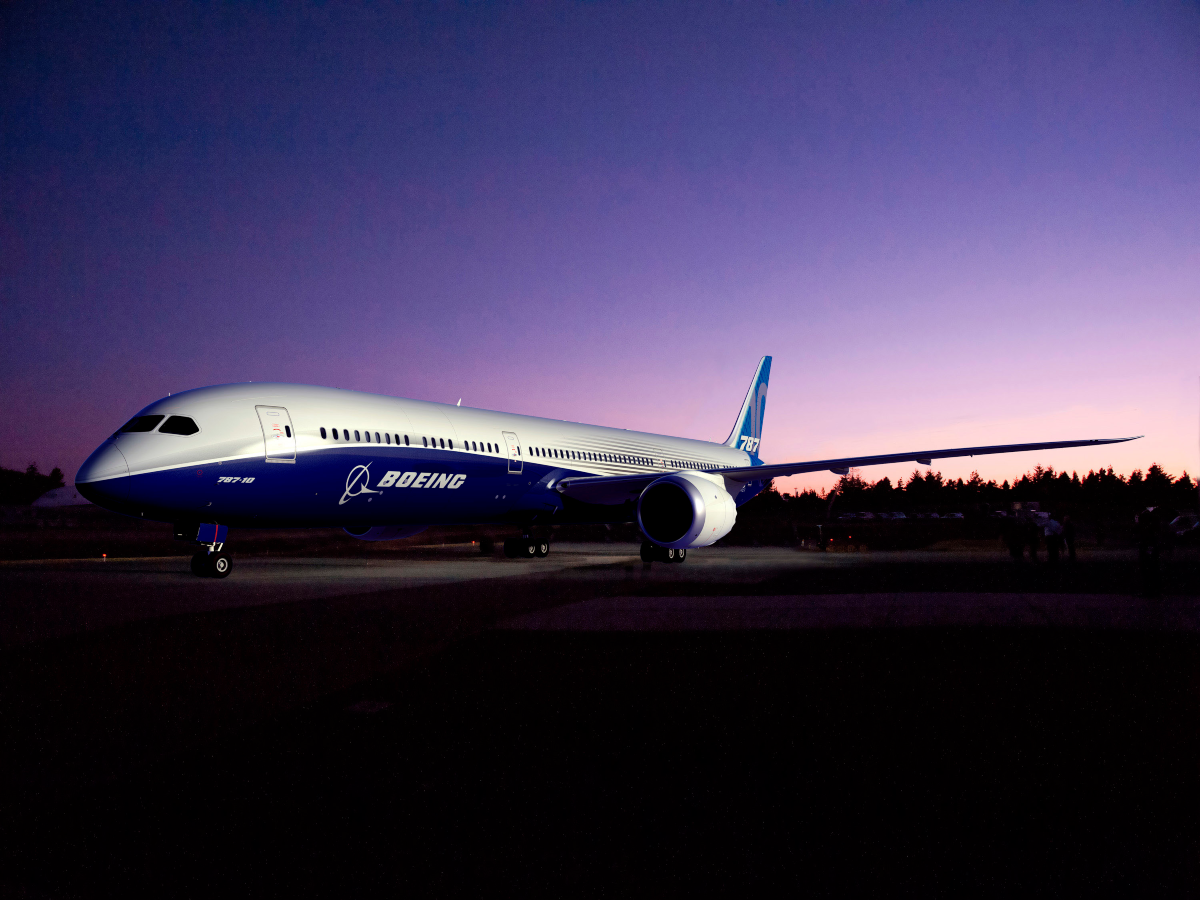
Related
Titanium Plates: Boeing Up Aginst A New 787 Dreamliner Issue
5
Improving commonality across the family
Making manufacturing changes to keep commonality for the 787-8
Date |
2018 |
---|---|
Area of concern: |
Manufacturing process |
Issue: |
Lower commonality for the 787-8 |
Fix: |
Structural design changes to improve commonality |
In order to enhance product value for operators, aircraft manufacturers try to maintain some sort of commonality among airliner families. This helps airlines save time and money since pilots and crew members can easily work on more than one specific type or variant of aircraft.
Photo: Boeing
As reported by Leeham News and Analysis, the Boeing 787-9 and -10 were designed with an impressive 95% commonality. However, the -8, which came before the others, had much less commonality. In order to rectify this, Boeing implemented manufacturing adjustments in 2018 that would see the Dreamliner variant’s structural design change to ensure it builds in a very similar way to the other two. As a result, customers could very easily operate two or three variants without much extra thought.
Have you flown on a Boeing 787? Which airline and route did you travel on? Share your experiences by commenting below.