The aviation industry is welcoming the idea of reviving supersonic transport. Since the unfortunate demise of Concorde, the viability of supersonic air travel has been being explored. From temperatures during a supersonic flight to the conditioning of air, supersonic transport (SST) interest among researchers and manufacturing has been increasing.
Specialized engines are required to power an aircraft that flies twice or even three times the speed of sound. While engines for a combat-type supersonic aircraft may be standard, there is a lot to learn about the complexity and performance of an SST engine.
Engine thrust
Olympus 593 Mk 610
- Compressor: Axial-flow, 7-stage low-pressure, 7-stage high-pressure
- Combustors: Nickel alloy construction annular chamber, 16 vaporizing burners, each with twin outlets
- Turbine: Two stages: one high-pressure, one low-pressure
- Fuel type: Jet A1
An aircraft engine creates thrust by taking the air in through the inlet and pushing it out at an accelerated speed. The engine thrust equals the air mass flow times the air mass overspeed. It is fairly simple in subsonic engines since the fan, compressor, and combustor can take inlet air at low subsonic speeds.
- Maximum thrust: wet: 169.2 kN (38,000 lbf) dry: 139.4 kN (31,300 lbf)
- Overall pressure ratio: 15.5:1 (with aircraft stationary)
- Overall pressure ratio: about 82:1 at Mach 2.0 (includes pressure rise in intake, 7.3:1, and in engine, 11.3:1 which is less than when stationary due to ram temperature rise)
- Air mass flow: (186 kg (410 lb))/s)
- Specific fuel consumption: 1.195 lb/(lbf⋅h) (33.8 g/(kN⋅s)) cruise / 1.39 lb/(lbf⋅h) (39 g/(kN⋅s)) SL (sea level).
- Thrust-to-weight ratio: 5.4:1
For supersonic speeds, however, the inlet scenario becomes rather complex. The aircraft’s maximum speed determines the necessary behavior of air intake on an SST. The inlet fan and compressor stages are unsuitable to take the inlet air faster than Mach 0.5, at which the tip speed is well over Mach 1.
Photo: Boom Supersonic
For a Mach 2.0 flight, the inlet air must be decelerated by Mach 1.5 before entering the fan and compressor. The air in the compressor section cannot exceed Mach 0.5, and the air in the combustor cannot exceed Mach 0.2 to prevent flame-out. For a Concorde-sized SST, an air mass of 220 lb (100 kg) must be decelerated every second by Mach 1.5 for the inlet and Mach 1.8 for the core flow.
SST inlet design (NASA)
- Supersonic Internal-Compression Inlets: The inlet must capture the airflow and decelerate it to subsonic speeds. An internal terminal shock system decelerates the flow to subsonic speed for the engine.
- Supersonic External-Compression Inlets: The inlet creates an oblique shock wave system on the exterior forebody of the inlet with a strong oblique or normal shock at the entrance of the internal ducting of the inlet such that subsonic flow enters the inlet.
- Supersonic Mixed-Compression Inlets: For flight above Mach 2, supersonic inlets perform a mix of supersonic compression between the inlet’s exterior and interior surfaces. An internal terminal shock system decelerates the internal supersonic flow to subsonic flow for the engine.
The SST engine intakes must be designed to continuously accelerate the air mass at supersonic speeds. Fixed normal shock inlets can work for SSTs that run below Mach 1.5. In other words, a flow speed reduction of nearly Mach 1.5 can be accomplished with a fixed inlet. Variable multi-shock inlets, such as the ones on the Concorde, are required for supersonic speeds approaching Mach 2.0.
Photo: Boom Supersonic
Variable inlets gradually decrease the speed of the incoming air before it hits the fan and compressor. While variable inlets cater to supersonic cruise speeds, the air must continue to flow through (and gets spilled overboard) during an engine failure. Failure to achieve that can result in tremendous instability due to drag created by the inlet.
Comparing the two existing SST designs, the Aerion AS2, with its proposed Mach 1.4 speed, uses a fixed inlet to manage airflow through the engines. On the other hand, the Boom Supersonic design must manage the incoming air using a variable multi-shock inlet.
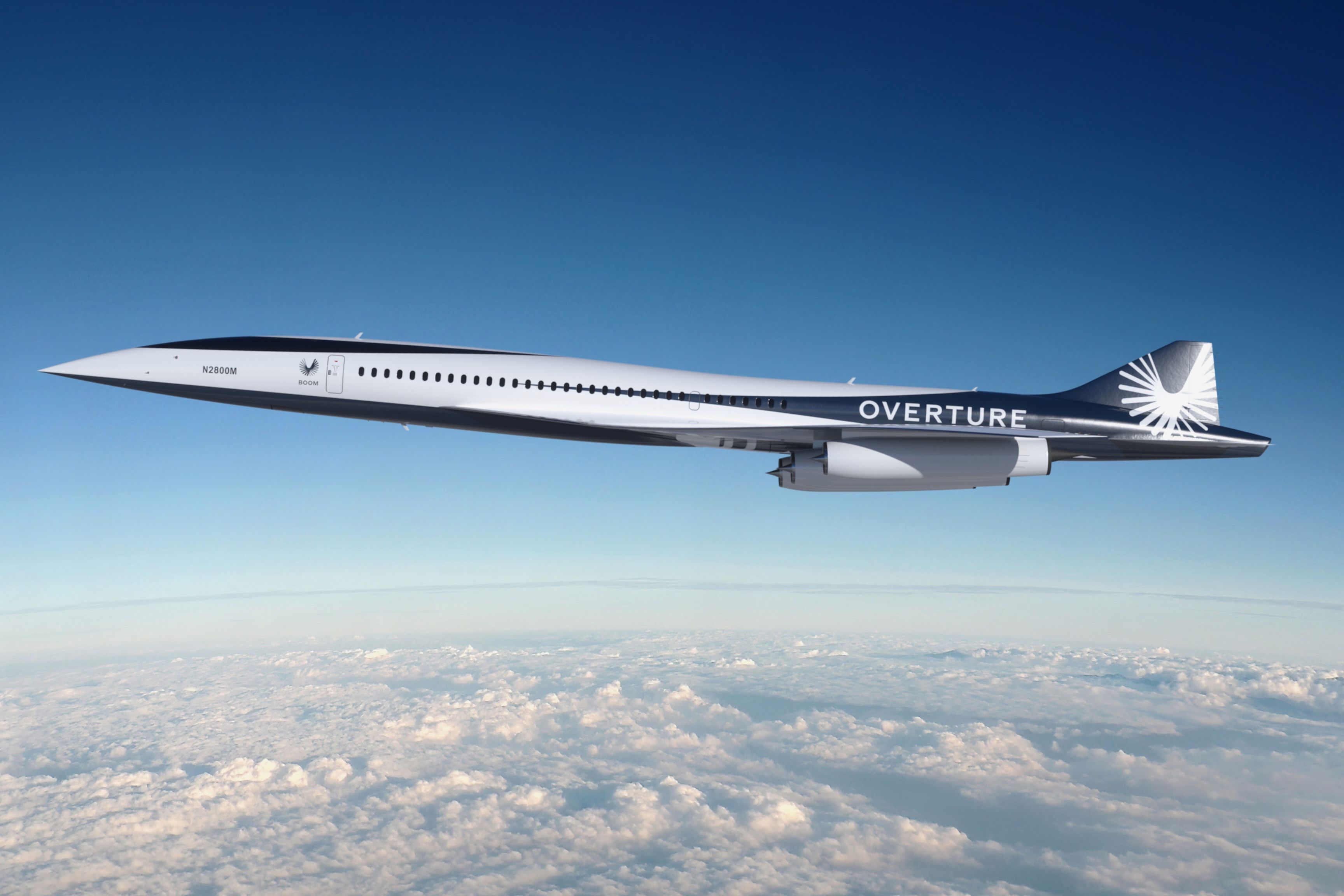
Related
Will Supersonic Flight Be More Accessible This Time Around?
Supersonic commercial flight is set to make an ambitious return by the time this decade is over. A major player in the game, Boom Supersonic, has sights for service entry by 2029. With the likes of American Airlines, United Airlines, and Japan Airlines placing orders for the Boom Overture, boarding one of these aircraft could be an option for your future journeys. One of the challenges of the Concorde program was its high costs, meaning that only those with large wallets could afford to fly the legend. However, I am hopeful that more passengers will be able to fly on supersonic aircraft during in this second coming. After all, in a previous interview with Boom, the company told me that tickets would be 75% cheaper than Concorde. Do you believe such savings could be made? Let us know below!
Inlet efficiency
Irrespective of the type of inlet, the force generated by the inlet to decelerate the air results in an opposing force called Ram air drag. The engine thrust must counter the airframe and Ram air drag at supersonic speeds.
This means that the engine not only takes energy from fuel to accelerate the air but also to counter the additional drag. Typical Mach 2.0 SSTs consume more than twice the fuel per generated thrust unit compared to a subsonic engine with the same efficiency.