If you were asked to name a pan-European aircraft manufacturer based in Toulouse, Airbus is likely to spring to mind immediately. And you would be right, of course, but it’s easy to forget that the European aerospace giant is not the only successful aircraft maker to call this southern French city its home.
In its 40 years of existence, ATR, a 50-50 joint venture between Airbus and Italian aerospace and defense group Leonardo, has managed to become the undisputed leader in the turboprop market.
AeroTime visited ATR’s HQ in Toulouse in mid-February 2025, just as the company was reporting its 2024 aircraft delivery figures and updating the media on the status of several of its major projects.
During the course of this visit, AeroTime also managed to get full access to the final assembly line (FAL) that supplies most of the world’s turboprop operators and catch a glimpse of how these small but super-efficient airliners take shape.
Turboprops are certainly a small market niche. For reference, ATR, which is the global leader in this market, has delivered 1,721 aircraft in the course of four decades, of which 1,351 were still active as of February 2025. Now, compare that with the 19,000+ A320-family aircraft delivered by Airbus since the late 1980s.
During the press conference held on February 12, 2025, ATR’s CEO Natalie Tarnaud Laude repeatedly highlighted the need for ATR to stay focused on its core value proposition.
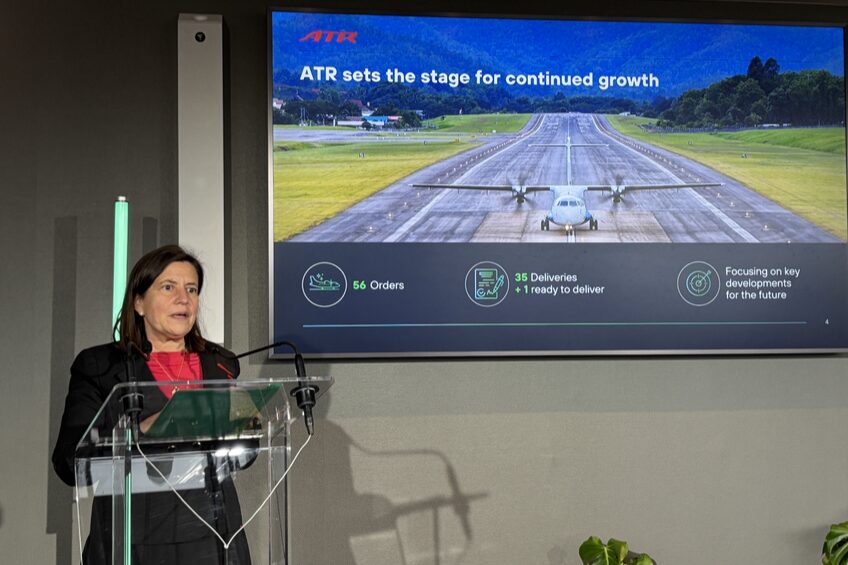
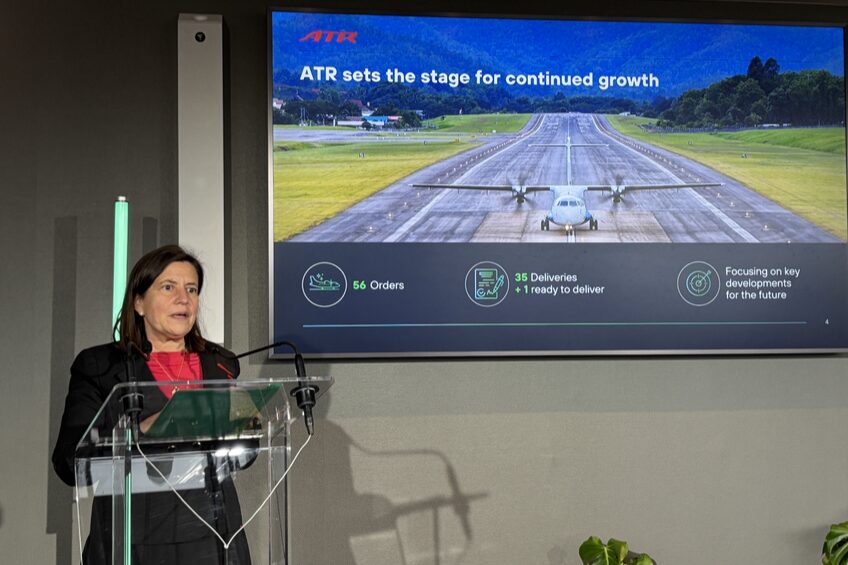
“We have a fantastic platform, which is super-optimized for the job it has to do,” she said, in reference to the fact that ATR is currently the only OEM able to offer a turboprop solution spanning the 50 to 70 seat market as well as the cargo segment.
In 2024 ATR logged 56 new orders, the vast majority (51 aircraft) of which were for the ATR 72-600 aircraft, with the rest going to the smaller ATR 42-600 model. This figure represents a 40% increase in the number of orders as compared to the previous year.
Over this period, ATR managed to deliver 35 aircraft (36, in fact, if we include one which was technically accepted by the customer but could not be physically delivered before the end of the year).
Remarkably, 80% of these orders were replacements for older ATR aircraft, something which demonstrates the degree of attachment some operators have to the company’s products.
In this regard, both Tarnaud Laude and Alexis Vidal, ATR’s Chief Commercial Officer, highlighted the growing collaboration between the manufacturer and a handful of leasing companies active in the turboprop space, which already account for around one quarter of ATR’s order book.
Lessors have often supported ATR in refining its value proposition and making the case for turboprops in front of prospective operators, Vidal explained. Another thing lessors do is provide capacity at short notice. This is particularly valuable at a time when production capacity is constrained by supply chain bottlenecks.
What next for ATR?
In 2025, Tarnaud Laude explained, ATR first expects to consolidate the pace of production achieved in 2024. Then, in the second half of the year, ATR will prepare to ramp up production by building stocks of key parts and components over time, to ensure that its production line doesn’t get stuck in bottlenecks.
However, not all recent developments at ATR have been positive.
The company has dropped or scaled down a number of strategic projects due to shifting market and technological conditions.
ATR cancelled its STOL program, which aimed to develop a version of the ATR 42-600 for short take-off and landing. Market feedback has not validated the initial hypothesis on which the program’s business case was originally built. A key factor here is that infrastructure investment, including runway extensions, in regions like southeast Asia has made the business case for this type of aircraft disappear.
Spinning the propeller’s green credentials
The EVO sustainable turboprop, designed to operate with 100% SAF and, further into the future, with hybrid-electric propulsion, has also been scaled down significantly.
Tarnaud Laude referred to the need to adjust expectations to reality. Without doubt, ATR remains committed to the EVO’s development and to continued work on a 100% SAF-compatible turboprop. However, this aircraft is going to be based on an evolution of the existing propulsion system rather than on a clean sheet engine.
In fact, ATR is already pitching its current technology as a ready-to-take low emissions, low noise alternative to jet aviation. ATR claims that its aircraft can deliver a 45% fuel saving reduction compared to jets of a similar size. To illustrate this point, ATR has two real petrol cans at its Customer Service Center, which a company representative invites guests to lift with their hands in order to gauge physically the amount of fuel per passenger that is saved on a typical 300nm-long flight.
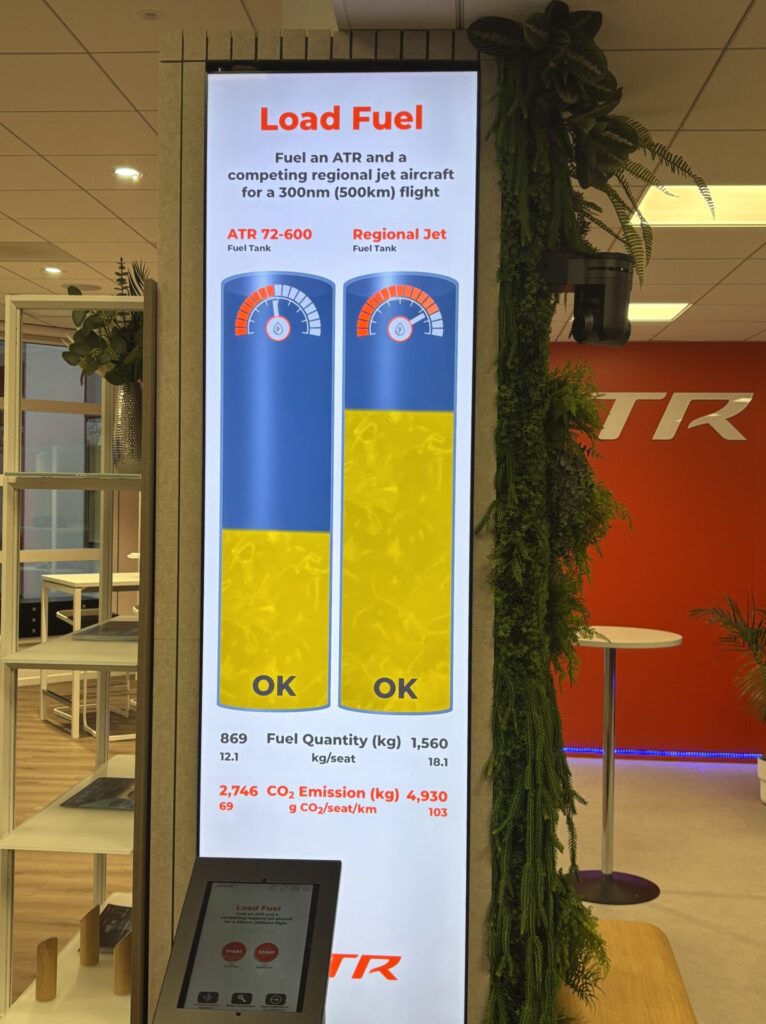
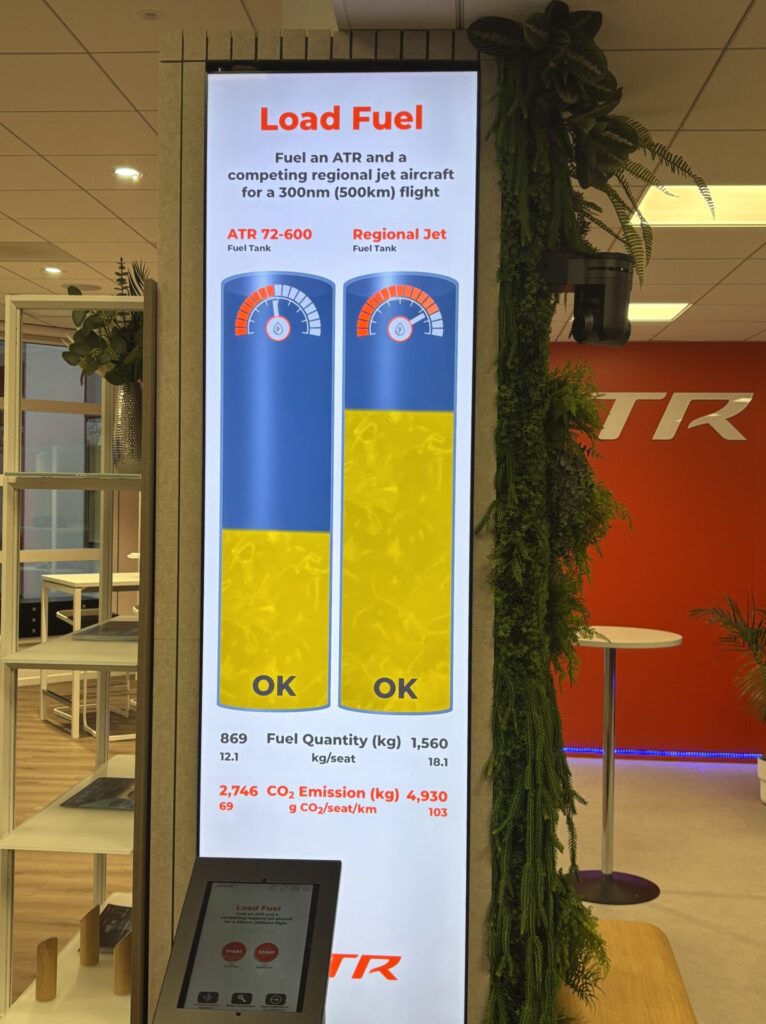
In response to journalists’ questions, Tarnaud Laude instantly dismissed other, purely hypothetical or exotic ideas for the long-term, such as the possibility of working on single pilot operations technology or even evaluating the feasibility of remotely operated aircraft for military applications.
ATR’s CEO remained adamant about the need to focus on what the firm already does well, particularly at a time when a large number of legacy turboprops are facing replacement within the next decade.
Tarnaud Laude highlighted this by pointing to the fact that ATR has a staff of only around 1,200, which is not a huge number by the standards of the commercial aircraft manufacturing industry. Airbus, in comparison, has over 90,000 employees.
Being a relatively small player, however, allows ATR to offer a very personalized service to its customers, something of which Tarnaud Laude and her team are particularly proud. This close relationship with many of its customers works both ways. An example given by Tarnaud Laude is the fact that, in 2025, ATR is focusing most of its investment on product improvements that have been suggested by customers’ feedback.
What remains on the table is ATR’s HighLine project, a portfolio of premium cabin concepts which are being pitched to upmarket operators, even some in executive aviation. These concepts could even be a vector to enter the US market in the future, by offering aircraft fitted with two or even three-class cabins.
ATR expects to deliver the first HighLine-fitted aircraft before the end of 2025. Malaysian operator Berjaya, which ordered two ATR 72-600s configured with 26 business class seats (even less than the standard 30-seat all-business class configuration proposed by ATR), is set to be the program’s launch customer.
AeroTime managed to get a close look at a full-size HighLine mock-up during a visit to ATR’s Customer Service Center.
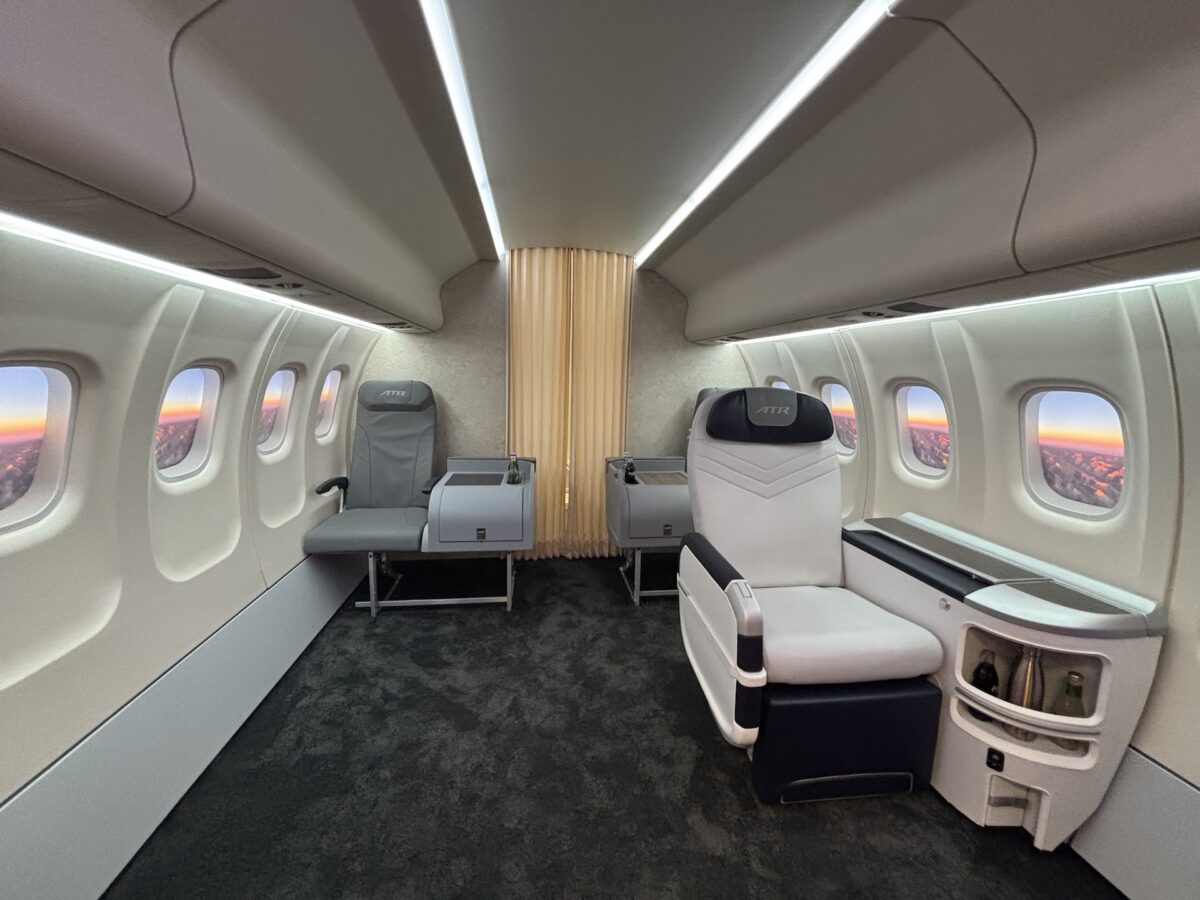
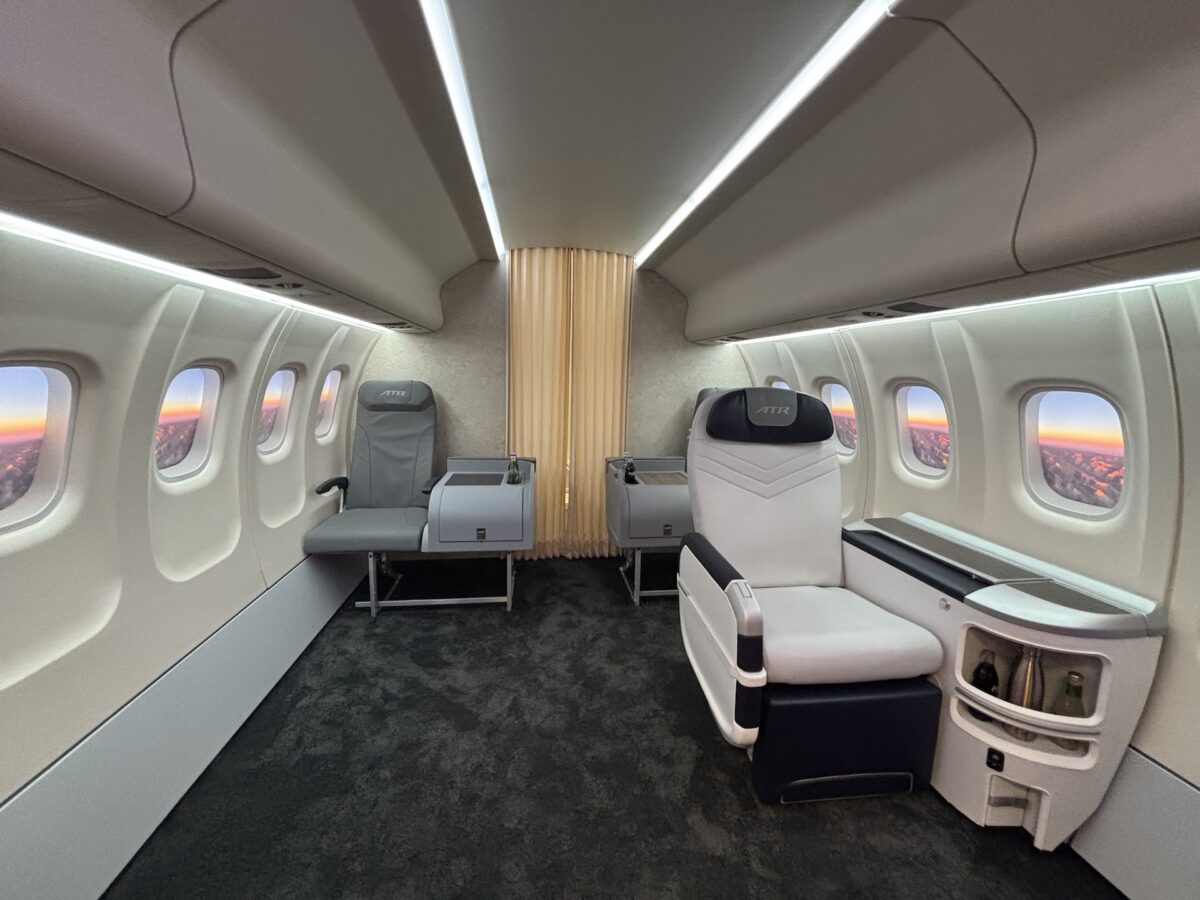
This included X-Space, which is an as-yet uncertified system to transform a regular two-abreast seat row into a single seat with a personal table for each passenger. This is achieved by removing the top part of one of the seats and attaching the table to the base of the seat. The whole procedure can be completed in under five minutes and can be used to turn a regular cabin into a premium one on a whim.
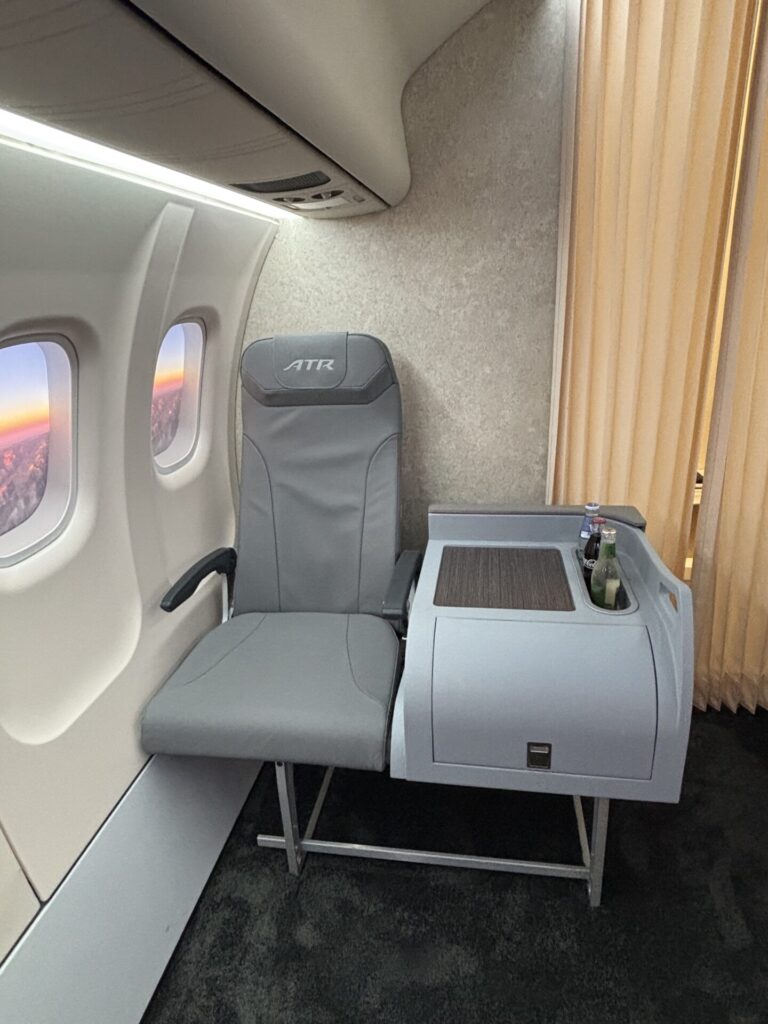
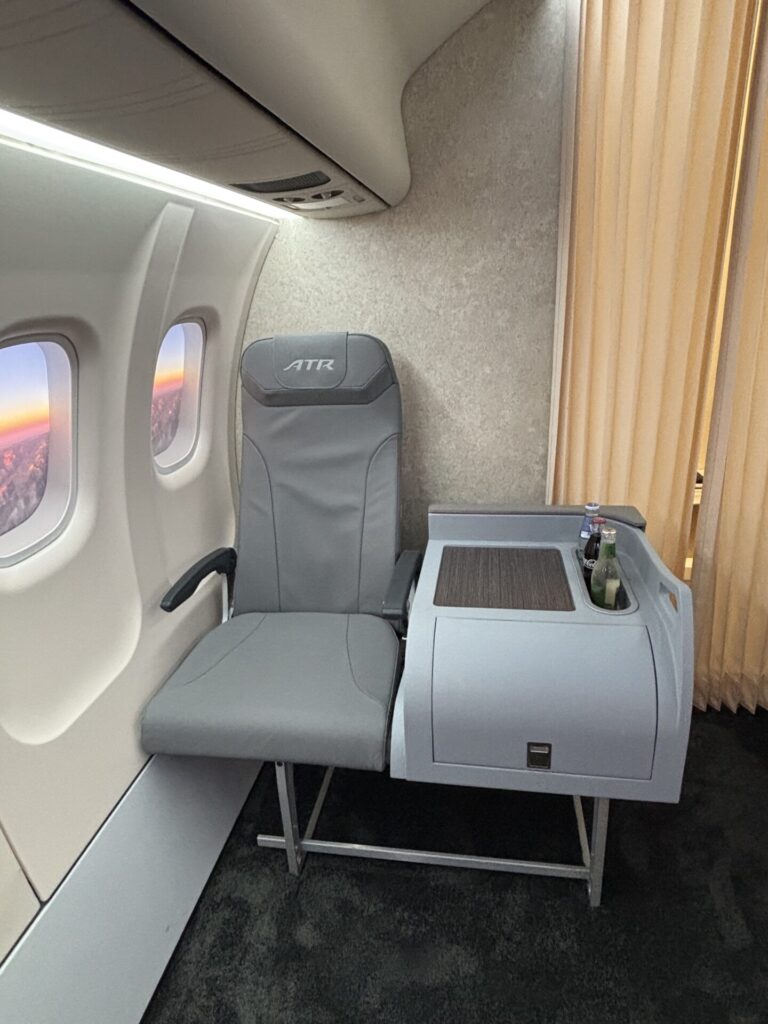
A tour of ATR’s Final Assembly Line
ATR’s final assembly line (FAL), is located at one of France’s most historical aviation facilities, which was built in the 1930s.
The building was used extensively during the Second World War by French aircraft maker Dewoitine. Later it hosted the production lines where iconic aircraft such as the Sud Caravelle airliner and the C-160 Transall military cargo aircraft were built.
The factory has since been thoroughly renovated and fitted with the latest technology. Today, it actually hosts three production lines.
Line A is for ‘green aircraft’. This is where the different structural elements are put together.
The fuselage and the appendage are made by Leonardo at two of its Italian plants, located in Pomigliano and Foggia in southern Italy, and then brought to Toulouse by boat and truck. The wings are made in Bordeaux, downriver from Toulouse.
After being assembled, the airframe moves onto Line B, where avionics are fitted and the aircraft interior is customized to meet the client’s requirements.
Finally, aircraft are moved outside to the flight line, to be thoroughly tested ahead of delivery.