Summary
- Twin-engine designs provide a balance of safety, performance, and efficiency for modern aircraft.
- ETOPS has expanded opportunities for twin-engine aircraft by ensuring safety on long flights.
- Twin-engine jets are designed based on two distinct configurations for both business and commercial operations.
Manufacturers have found a perfect balance between flight safety, performance, and efficiency in a twin-engine aircraft design. On the one hand, two engines are better than one in terms of safety through redundancy. On the other hand, the emergence of Extended Range Twin Operations approval (ETOPS) has enabled the use of twin engines as opposed to three or four engines.
ETOPS are safety standards set by the International Civil Aviation Organization (ICAO) that permit twin-engine aircraft to operate over a route containing a point further than one hour of flying time at the approved one-engine inoperative cruise speed.
The early days
The early days of aviation saw abundant single-engine aircraft, primarily due to power requirements. Most small airplanes featured a single turboprop in the front of the aircraft, being solely responsible for generating the required power. In April 1941, the German fighter prototype, Heinkel He 280, became the first official twin-engine aircraft to take to the skies. The aircraft featured a pair of Heinkel HeS 8 axial-flow turbojet engines.
In 1954, Cessna built the first twin-engine private jet, the four-seat Model 310. Featuring wingtip tanks, the aircraft could reach a maximum speed of 230 mph thanks to a pair of 240-hp engines. In 1953, aviation authorities in the US introduced a “60-minute rule” that restricted the use of twin-engine aircraft to a 60-minute diversion area.
In commercial passenger aviation, the prominent early aircraft to feature twin engines were the McDonnell Douglas DC-9 and the Boeing 737. Both types were developed independently in the 1960s and featured Pratt & Whitney JT-8 low-bypass turbofan engines. The twinjet configuration was primarily used for short-range, narrow-bodied aircraft with a limited payload capacity.
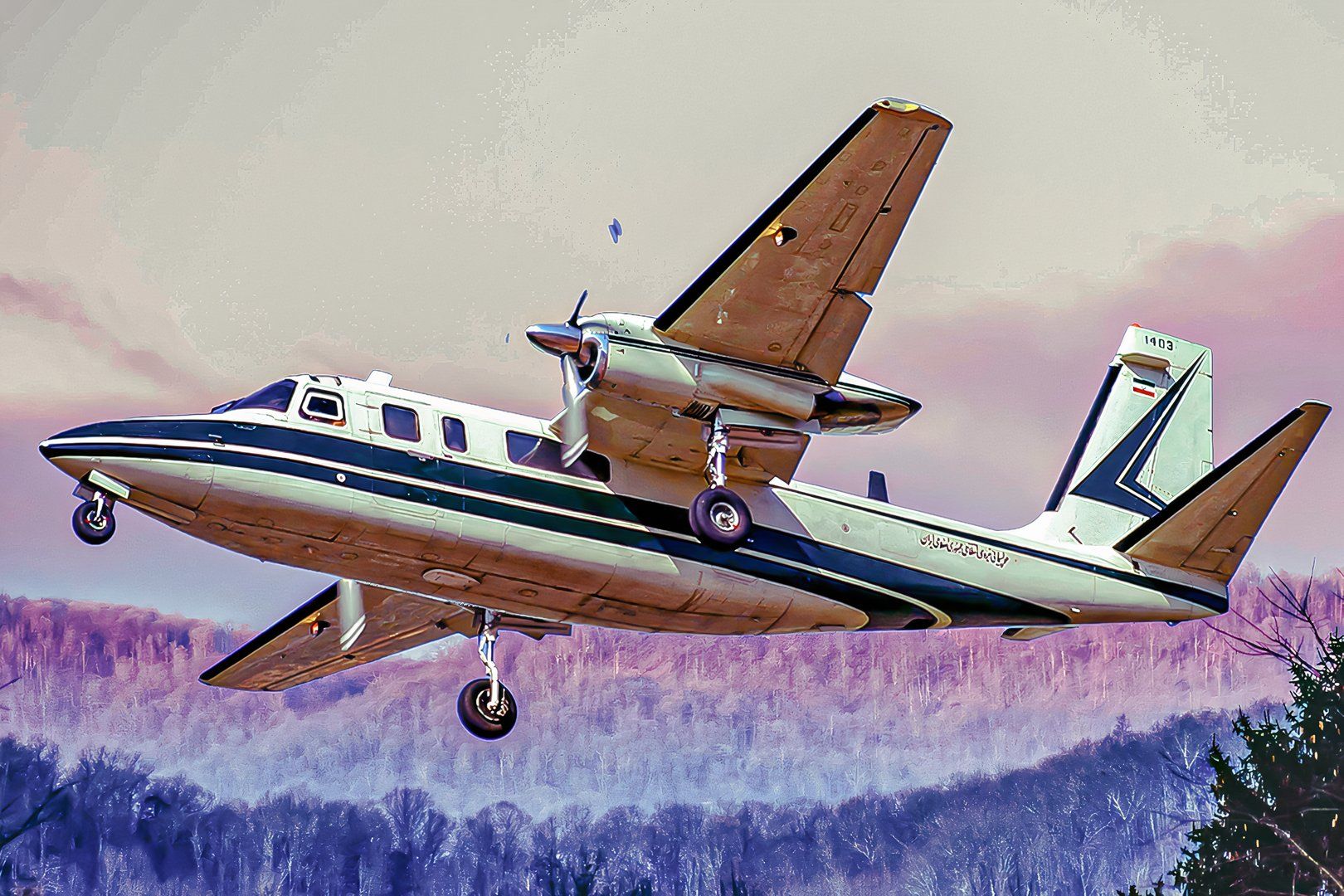
Related
The First Metal Twin Engine Aircraft: A Look At The Aero Commander
The first all-metal twin-engine airplane.
Three- and four-engine designs
Before the introduction of ETOPS, aircraft manufacturers explored various three-engine and four-engine designs. While the primary purpose was to enable long-distance over-water flights, the increased thrust also supported larger airframes, accommodating 300 or more passengers. With the reliable performance of jet engines, particularly the PW JT-8D, the 60-minute rule was waived for three or more-engine aircraft.
Photo: InsectWorld | Shutterstock
The decision paved the way for many intercontinental tri-jet designs, including the Lockheed L-1011 Tristar and McDonnell Douglas DC-10. While twin jets were still restricted to the 60-minute rule, three-engine and four-engine jets ruled the long-haul skies until the late 1980s.
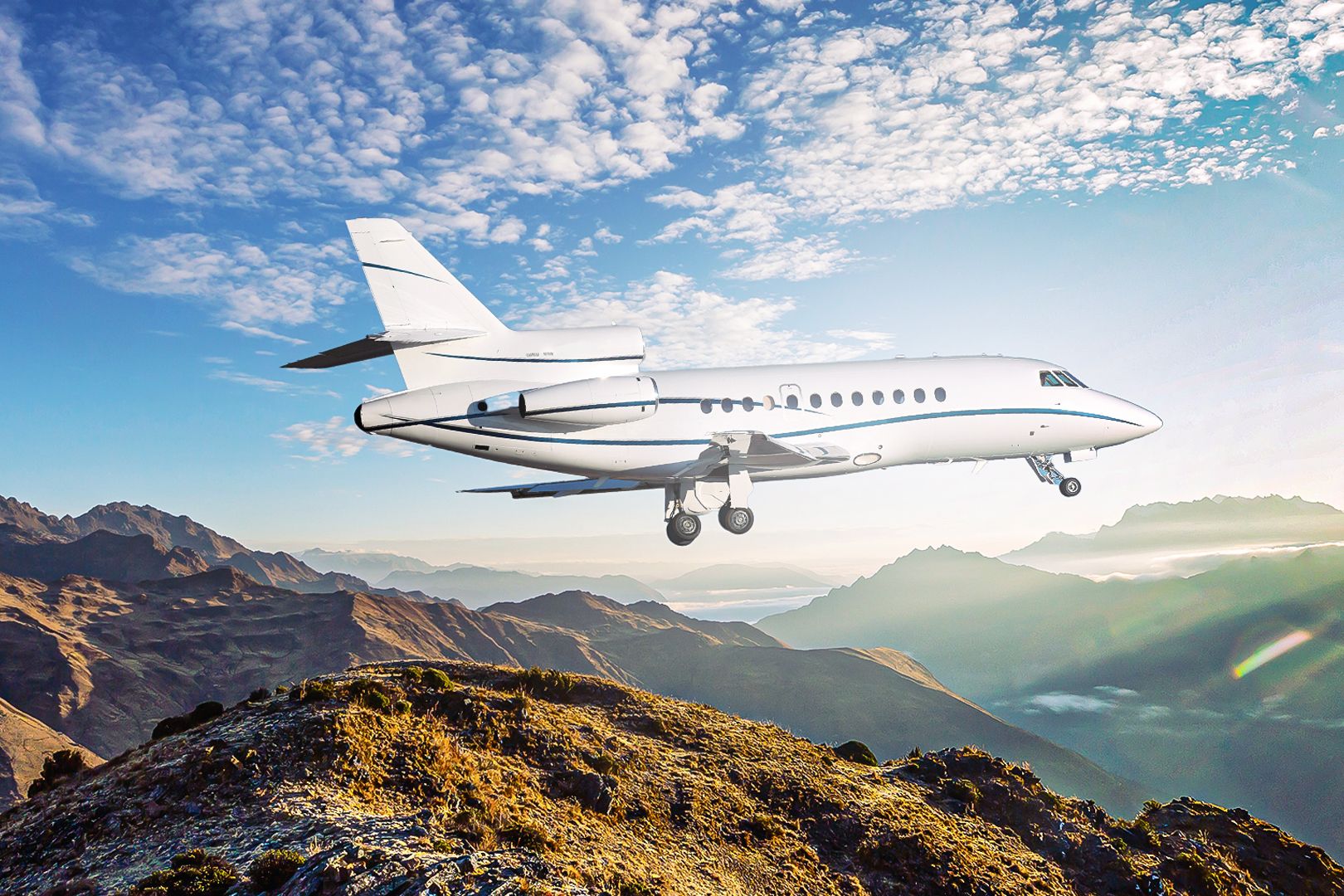
Related
A Guide To The Dassault Tri-Jet Family
Dassault is known for its production of business jets with three engines.
How ETOPS enabled more twin-engine aircraft designs
The two most common twin-engine configurations are:
- At the rear of the fuselage: Most modern business jets, including ones from Gulfstream, Bombardier, and Cessna, have this configuration. Some regional passenger jets, such as Boeing 717/MD-95 and CRJ-700/900, also feature rear-mounted engines.
- Engines are attached under the wings using pylons: Most commercial passenger narrowbody and widebody jets feature this configuration. Some examples include the Airbus A320, Airbus A350, Boeing 787, and Boeing 777.
ETOPS rules introduced twin-engine jets to fly distances previously out of limits. The ETOPS regulations dictate that a twin-engine aircraft must be able to reach an alternate airport safely even after one engine has failed. Notably, producing sufficient power for an economical flight is not the main concern when one engine has failed.
Instead, the other engine can generate sufficient thrust until an emergency landing at the nearest deviation point is done. ETOPS certification allowed manufacturers to focus more on design and maintenance requirements rather than thrust performance requirements in normal conditions.
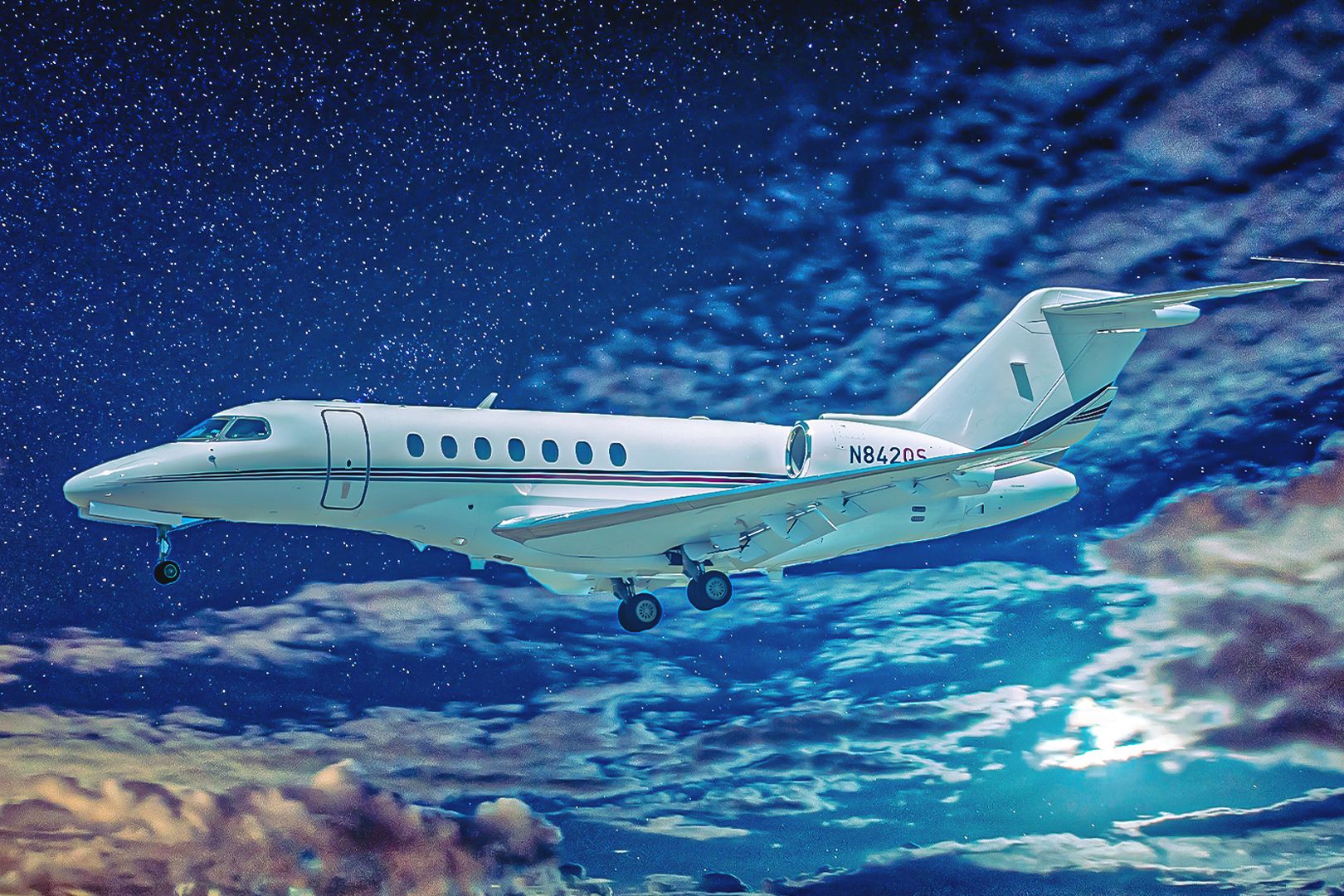
Related
The 4 Most Expensive Cessna Citation Jets
The prices of Citation family jets are at par with the competition.
One of the major components of ETOPS certification is that the failure of one engine does not cause failure to the other, and the failed engine can be cut from the operational system. According to AOPA,
“In twins with propellers that both rotate clockwise when viewed from the cockpit, the left engine is critical. If this engine fails, the yaw created by the operating right engine is exacerbated by P-factor.”
Regardless of how many propellers an airplane has, each one produces P-factor, especially at low airspeeds and high angles of attack.
As such, independent systems had to be built and maintained to ensure the twin-engine aircraft continued to perform within its design limits (in normal conditions) while complying with ETOPS requirements in case of a single-engine failure event.
ETOPS ratings are permitted based on aircraft (and engine) capability. For example, an aircraft certified for ETOPS-180 can fly within three hours (180 minutes) of single-engine operations at a diversion point. The current ETOPS ratings are:
- ETOPS-75
- ETOPS-90
- ETOPS-120/138
- ETOPS-180/207
- ETOPS-240
- ETOPS-270
- ETOPS-330
- ETOPS-370
Today, apart from a handful of Dassault Falcon tri-jets, most modern private jets are configured with two engines. The advanced materials and machining techniques have enabled much greater engine power and efficiency, thereby making twin-engine operations sufficient for even some of the largest commercial and private jets.
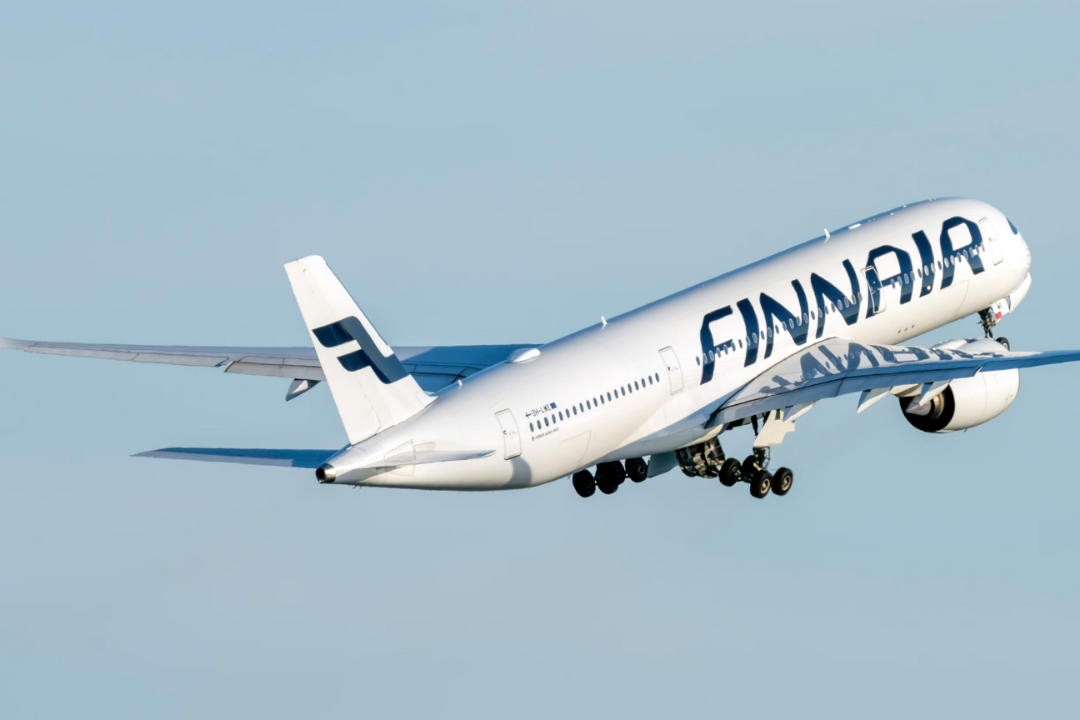
Related
How Far Can Modern Twinjets Fly After A Single Engine Failure?
Twin-engine jets can fly for at least 60 minutes and up to 6 hours on one engine.